
Vídeo: "Milagres" de tecnologias de Pedro, o Grande ou por quem os sinos dobram
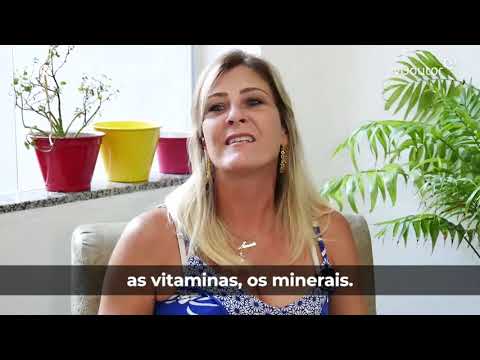
2024 Autor: Seth Attwood | [email protected]. Última modificação: 2023-12-16 16:14
Um artigo do meu associado.
"Se os fatos contradizem a teoria, você tem que jogar fora a teoria, não os fatos."
A. Sklyarov
Ninguém fica indiferente e os magníficos vasos de pedra do Hermitage conquistam para sempre com a sua beleza e fantástica execução. Jaspe, granito, malaquita - a variedade de materiais e cores impressiona. E as dimensões sólidas dos vasos, os elementos invulgarmente complexos e o perfeito polimento da superfície levantam muitas questões sobre as tecnologias da época. Vamos caminhar dos corredores de l'Hermitage às oficinas de produção e ver como era possível fazer produtos tão perfeitos, tendo uma gama bastante limitada de materiais de produção e soluções técnicas.

Para isso, fui especialmente para l'Hermitage. Com cuidado, mais uma vez, examinei as peças expostas e também encontrei sinais sobre o "fabricante". Assim está escrito: "Fábrica de lapidação de Yekaterinburg". Pare! O que o corte tem a ver com isso?
Granil é (do italiano graniglia - migalhas, grânulos) um nome geral para copos de uma composição especial triturada até um determinado tamanho. A faceta é usada para decorar ladrilhos de cerâmica, granito cerâmico. O armazenamento pode ser brilhante ou fosco, transparente, suave, branco ou colorido, com lustre ou efeitos metálicos, etc. Eles podem ser usados para criar um efeito visual e para fornecer certas propriedades. O que o vidro tem a ver com isso? Falarei sobre isso algum tempo depois, em outro artigo. E a história oficial diz que cortar e lapidar são as mesmas raízes. E ainda mais - eles têm o mesmo significado! Bem, que seja, eles também estudaram isso em instituições especiais, entre elas há doutores e professores de ciências históricas e outras ciências. E somos pessoas simples. Então, mais longe. Acontece que naquela época havia três fábricas de corte e retificação.
Em Yekaterinburg, em Kolyvan em Altai e em Peterhof perto de São Petersburgo. Você pode ler sobre essas fábricas na Internet. As máquinas de moagem eram movidas por moinhos de água. Não encontrei nenhuma informação sobre rebolos. Por que e como os abrasivos foram criados para polir materiais tão duros, não sabemos. Mas eles fizeram as colunas e os vasos! Então fizemos os abrasivos também. Mas é surpreendente que, para tais indústrias, muitos desses consumíveis sejam necessários, além disso, de diferentes tamanhos de grãos. E para isso, por sua vez, você precisa de uma produção e propriedade de tecnologia consideráveis em separado. Afinal, os materiais abrasivos (aqueles com os quais se lixam e polem) devem ser mais duros. E seu processamento não é uma tarefa fácil. E não há menção disso em lugar nenhum. Vamos fechar nossos olhos para isso também. Após a revolução de 1917, as fábricas de Kolyvan e Yekaterinburg cessaram a produção, restando apenas as fábricas de Peterhof, que depois de 1947 foram bastante modernizadas. Ainda, mais corretamente, um novo foi construído! A água era fornecida por um tubo de ferro fundido, havia 2 turbinas de 15 cavalos cada, e assim por diante. Como era a produção antes disso? Para fazer isso, você precisa visitar o museu na fábrica Kolyvan. Há até um moedor de simulação lá! Vamos considerar esse layout.

Então este é o progenitor do torno! É assim que a história oficial explica a criação de colunas para a Catedral de Cristo Salvador em Moscou e até para a Catedral de Santo Isaac! Tudo é fácil e simples! O moinho de água gira as engrenagens, elas acionam o eixo com acionamento por correia, e esse, por sua vez, o eixo do progenitor do torno. Mas os cálculos da engenharia estão trazendo sua própria mosca na sopa para este doce barril de mel. As colunas da Catedral de Cristo Salvador tinham mais de três metros de comprimento, e ainda mais para a Catedral de Santo Isaac. E ao calcular o peso dos espaços em branco, temos um problema - cada espaço em branco tem pelo menos mais de 2 toneladas.
O modelo já está instalado no modelo. Como um eixo de madeira sustenta um bloco de pedra tão pesado? Nos tornos modernos, um dispositivo muito poderoso é usado para prender uma peça (um mandril), e não apenas aperta a peça nas pontas, mas também a prende com "dedos" como um polvo!

Mandril de torno

A parte A fixada no modelo é simplesmente fixada em ambos os lados por um eixo de madeira. Não vamos discutir, é apenas um layout, vamos fechar os olhos para isso. Vamos fechar nossos olhos para o fato de que um dos eixos de fixação deve se mover horizontalmente. Como primeiro "afastar" e, depois de instalar a peça de trabalho, "apertá-la".

E na maquete é mostrada uma retificadora rígida, já com uma parte fixa. Não vamos encontrar falhas no diâmetro dos eixos da mesma forma. Costumava haver outras árvores, árvores fortes. Deus os abençoe, com esses erros. Mas o que não é perdoado pela resistência aos materiais e à engenharia é um erro de cálculo no atrito. Neste caso, o acionamento por correia deve girar uma peça de trabalho pesando 2 toneladas ou mais! E tudo à custa do moinho de água. Sem levar em conta que as próprias superfícies de madeira serão lixadas pela correia, a já baixa eficiência cairá ainda mais. Mas pode-se presumir que, se necessário, o eixo e as correias foram trocados com o tempo. Mas o principal erro de cálculo deste layout (e, conseqüentemente, de toda a tecnologia proposta) são os eixos sobre os quais a peça girou! Sob o peso da peça, nos pontos de rotação dos eixos, o atrito é tão grande que são necessários esforços titânicos para fazê-los girar.
Se, para facilitar o torque, abrirmos um espaço entre o eixo e a coluna vertical, o eixo não mais segurará a peça e ela cairá. E se forçarmos sua rotação, a carga nos eixos de madeira funcionará por um mínimo de tempo (de acordo com estimativas preliminares, não mais do que 10 minutos). Conclui-se que este moedor não funcionou. E, portanto, foi neste moedor que as colunas de todas essas catedrais não foram feitas.

Agora vamos olhar para outro moedor. A partir de um grande eixo, um acionamento por correia girava pequenos eixos fixados em pêndulos de madeira suspensos e transmitindo torque ao rebolo. Tudo é fácil e simples de novo? Não! Para transferir a rotação, a correia deve sempre ser mantida esticada. E então descobrimos que só podemos moer na distância da correia tensionada. Além disso, somos obrigados a fornecer a tensão da correia com nossas mãos. Ao mesmo tempo, certifique-se de que o rebolo seja pressionado contra a peça de trabalho. A velocidade de rotação do moinho de água era em média 60 a 150 rpm! O instrumento moderno tem cerca de 1000.
Eu nem mesmo acho falha no método de transferência da rotação para o segundo rebolo (que a estatueta está segurando em uma camisa vermelha) - o diagrama para girar a correia em 90 graus não é mostrado (e isso requer um dispositivo especial, mas levando a uma perda adicional de eficiência). No mínimo, você pode triturar com este dispositivo. Mas apenas em linha reta. E movendo constantemente a peça de trabalho para frente e para trás. E o processo de polimento envolve pelo menos 10 passadas sucessivas com diferentes tamanhos de grãos abrasivos! Agora uma pergunta! Como polir um vaso? Torcer, girar e inclinar? Ou seja, acontece que os produtos, às vezes atingindo várias toneladas, se moviam no espaço como o mestre queria? Portanto, este moedor não poderia polir vasos de l'Hermitage! Os cálculos preliminares foram realizados usando programas especiais de engenharia. Esses programas são usados para criar mecanismos modernos de alta tecnologia. Todas as aplicações simuladas desses moedores deram respostas negativas. Além disso, ao estudar o mecanismo dessas retificadoras, muitas deficiências não foram levadas em consideração (e sempre a favor da história oficial!). E alguns deles, como a falta de produção de materiais abrasivos, a dureza de alguns materiais processados é próxima em dureza ao granito (e isso já é um problema muito grande!), A impossibilidade tecnológica de polir e moer elementos complexos de vasos (bordas convexas, ranhuras, pétalas) geralmente se reduz a não haver operabilidade desta tecnologia neste assunto. Essa tecnologia pode ser chamada com segurança de "conto de fadas de Munchausen". Visitantes de museus não versados em detalhes técnicos ouvem as histórias coloridas dos guias com o esquecimento.
É mais fácil acreditar que “foi feito com facilidade” e seguir silenciosamente para a próxima exibição, do que se opor e ter medo de olhares de esguelha e conversas, como se você ousa argumentar - todo mundo acredita, e você é tão inteligente aqui? Aqui está como eles nos contam sobre a entrega de um vaso czar de 19 toneladas do vaso de moagem de Kolyvan para São Petersburgo: “Em 19 de fevereiro de 1843, um trem de cavalos atrelados a um trenó especial (de 154 a 180, dependendo no terreno) levou a tigela de Kolyvan para Barnaul, depois para o cais Utkinskaya do rio Chusovaya. Carregamos a tigela em jangadas em detalhes e seguimos ao longo do rio Chusovaya até o rio Kama, do rio Kama ao rio Volga, ao longo do rio Volga com caminhões de barcaça, depois ao longo do canal de desvio para o rio Neva”. Primeiro, eles fizeram um trenó especial (perderam tempo, esforço, materiais) e arrastaram 150-180 cavalos em equipe. Com tantos cavalos, temos um problema de sincronicidade. E então, tendo chegado ao rio, a tigela foi desmontada em suas partes componentes e desmontada em jangadas.
Cadê a lógica ??? Nós rolamos um quadrado, nós usamos um redondo. Por que, mesmo quando crianças, duvidamos da veracidade das histórias do Barão de Munchausen e, crescendo, acreditamos em tal absurdo? Se o vaso era dobrável, por que quebrar um monólito de mais de 30 toneladas, arrastá-lo pelas montanhas e ravinas, e então fazer não um vaso sólido, mas com partes ??? “A obra começou em fevereiro de 1828. Com a ajuda de 230 operários, a pedra foi puxada para o galpão de alvenaria e elevada a um metro de altura. Cerca de 100 artesãos estavam envolvidos no processamento primário do monólito, após o qual em 1830 a pedra foi colocada sobre os troncos e manualmente, com a ajuda de 567 pessoas, transportou o bloco 30 verstas para Kolyvan. 567 pessoas arrastaram o monólito, para que depois, já na fábrica, o partissem em pedaços. CINCO CEM SESSENTA E SETE PESSOAS !!! Eles arrastaram o caroço. CEM OITAVA CAVALOS !!! Eles arrastaram um vaso. Como isso soa ?! Plausível! E então, após tais esforços, eles foram desmontados em partes e carregados em jangadas …
Isso é tudo. Toda saúde e uma mente brilhante!
Recomendado:
Por que os sinos eram executados nos velhos tempos?

No final do século 16, um evento muito, muito estranho aconteceu na cidade russa de Uglich. Uma enorme campainha de alarme foi puxada para a praça da cidade. Um ferreiro especialmente convocado na frente de todas as pessoas honestas cortou o sino da "língua"
Pedro I: Grande soberano ou obsceno e bêbado?

Após o trabalho de mudar a Rússia, Pedro, o Grande, divertiu-se, organizando uma bebedeira grandiosa. O resto do czar, bem como suas reformas, os súditos olhavam com horror
Quem alimentou quem na URSS e quem perdeu mais com seu colapso

Um quarto de século após o colapso da URSS, ainda não conseguimos entender por que isso aconteceu? De fato, na primavera de 1991, 77,7% dos cidadãos votaram em referendo pela preservação de um único país. E no final do mesmo ano, aproveitando a derrota do Comitê de Emergência Estadual, muitas repúblicas sindicais instantaneamente prepararam seus próprios votos em cidades pequenas, nas quais as pessoas já exigiam independência. Por exemplo, na Ucrânia, aqueles que queriam viver separados do resto da União representavam 90%! E na Armênia - até 99%
Os russos não se dobram: eles se encontraram na aldeia e não querem voltar

Victor, um freelancer, cresceu em uma vila siberiana e voltou da cidade depois que o regime de auto-isolamento foi introduzido. Dirige um videoblog sobre a vida rural
Não há aquecimento? Quem está por trás do grande golpe climático

Acontece que histórias assustadoras sobre o aquecimento global são apenas parte de uma grande guerra no mercado de energia